Local Pickup FAQ's
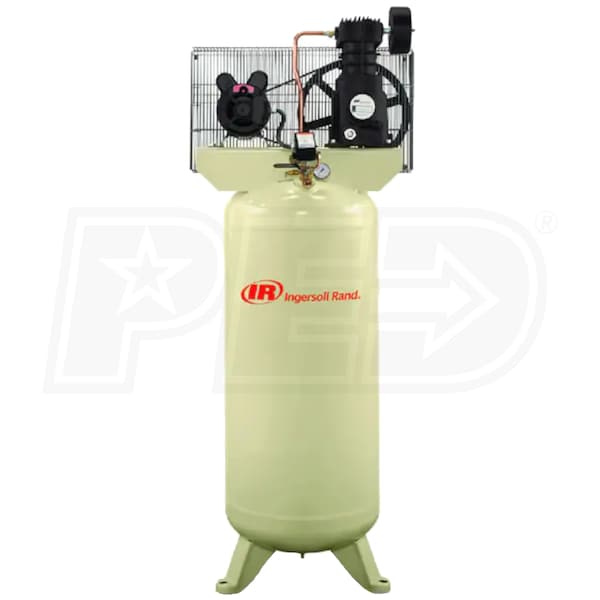
Hover to zoom
1 Of 5
Ingersoll Rand 5-HP 60-Gallon Single-Stage Air Compressor (230V 1-Phase)
Model:
SS5L5
+
Share This Product
Recommended Accessories

Expert Recommended Accessories
Selected by Melissa, our Expert
Required Accessories
9
These accessories are required to properly setup/install this product.
Optional Accessories
10
Features
Grade
Consumer
Style
Single Stage 1-Phase
CFM
18.1
Tank Size
60
- 100% Cast-Iron Cylinders and Frame
- Designed for the toughest 100% continuous duty applications
- Manual Thermal Overload Protection
- No magnetic starter needed and protects motor from damage
- Oil Sight Gauge
- Easily check compressors pump oil level
- OSHA Compliant
- Fully enclosed flywheel, belt and motor sheave
- Fully Tested
- All units are prewired and thoroughly tested prior to shipment
- American Pride
- Proudly built in the U.S.A.
- 1-Year Warranty (Unit Ships Dry)
- 2-Year warranty available with purchase of the Ingersoll Rand SS3 Electric Air Compressor Start Up Kit (Model: 20100251) at time of purchase
California residents see
WARNING: Cancer and Reproductive Harm - www.P65Warnings.ca.gov.
For more information go to: www.p65Warnings.ca.gov
Specifications
SS5L5
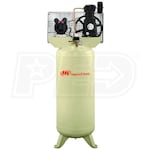
General Information
Product Category
Air Compressor - Stationary
Motor
Voltage
230 Volt AC
Phase
1-Phase
Magnetic Starter
Magnetic Starter
The Magnetic Starter is the "thinking cap" for the motor of the air compressor. Magnetic starters are electromagnetically operated switches that provide a safe method for certain motors to be started under a large motor load.
No
Amp Draw
21.5
Recommended Breaker
Consult Certified Electrician
Engine
HP
5
Pump
CFM
CFM
Cubic Feet Per Minute, which indicates the compressor's flow rate - or the amount of air that a compressor can produce at a given pressure level. Typically compressors that have higher CFM ratings are able to provide more air, which makes them ideal for larger applications
18.1
CFM Rated @
90 PSI
Pump Material
Solid Cast Iron
Max PSI
Max PSI
PSI, or Pounds Per Square Inch, measures the amount of pressure placed on a square inch of space. In compressor terms, PSI is the amount of force that an air compressor can deliver
135 PSI
Oil Sight Glass
Yes
Pump Type
Single-Stage
After Cooler
After Cooler
An aftercooler is a mechanical heat exchanger designed to remove the heat and moisture of compression from a compressed air stream so the air is cool and dry enough for use in air-operated equipment. A compressed air aftercooler has three primary functions: Cool the air discharged from the air compressor
No
Pump Drive
Belt Drive
Oil Type
Oil Lubricated
Oil System
Splash Lubricated
Pump Low Oil Shut-off
Pump Low Oil Shut-off
Prevents the air compressor from operating or restarting without an adequate amount of oil in the compressor
No
Tank
Tank Size
60 Gallons
Tank Outlet
1/2 Inch
Electronic Drain Valve
Electronic Drain Valve
The inexpensive and reliable electric drain valve (EDV) automatically removes condensate from your air system. It has an integral strainer to prevent clogging and saves time and money by eliminating the need for manual draining
No
Tank Orientation
Vertical
Filter
Regulator
No
Accessories
Pressure Gauge
Yes
Air Dryer
No
Overview
Product Category
Air Compressor - Stationary
Weight
310 Pounds
Certification
UL/CSA/ASME
Consumer Warranty
1 Year
Commercial Warranty
1 Year
Product Length
20 Inches
Product Width
30 Inches
Product Height
71 Inches
Power Type
Electric
UPC
678384031721
Reviews
(14)
Ingersoll Rand SS5L5 Reviews & Ratings
Product Q&A
(2)

Product Questions
Answered by Melissa, the Air Compressor Expert
How many amps does the SS5L5 pull?
Mike Work
from Texas
October 11, 2016
Hi Steve, looking at the IR SS5L5 single stage and the Quincy 2V41C60VC two stage. Wanting to run a plasma cutter and a sand blaster and not sure which would be better. The IR produces more CFM but the Quincy has higher maximum PSI. Also want to run various air tools in my shop. What are the pros and cons for single vs two stage? Which would you suggest for my needs? Thanks
Steve Wang
from Oklahoma
December 30, 2014
How-To Articles
How to Pick the Perfect Single-Stage Compressor
Some homeowners need air compressors occasionally for inflating tires, running ...
How To Quickly Improve Your Gas Mileage
You don't have to be a rocket scientist to figure out properly inflated tires w...
Modern Air Compressors for Modern Dentistry
It's difficult to earn a patient's trust. After years of investing in your prac...
Manuals
Ask A Question!
*Required Fields
+
Thank You For Submitting Your Question
Your submission has been sent successfully. Please give our experts up to two business days to respond.

Media Gallery
Ingersoll Rand 5-HP 60-Gallon Single-Stage Air Compressor (230V 1-Phase)
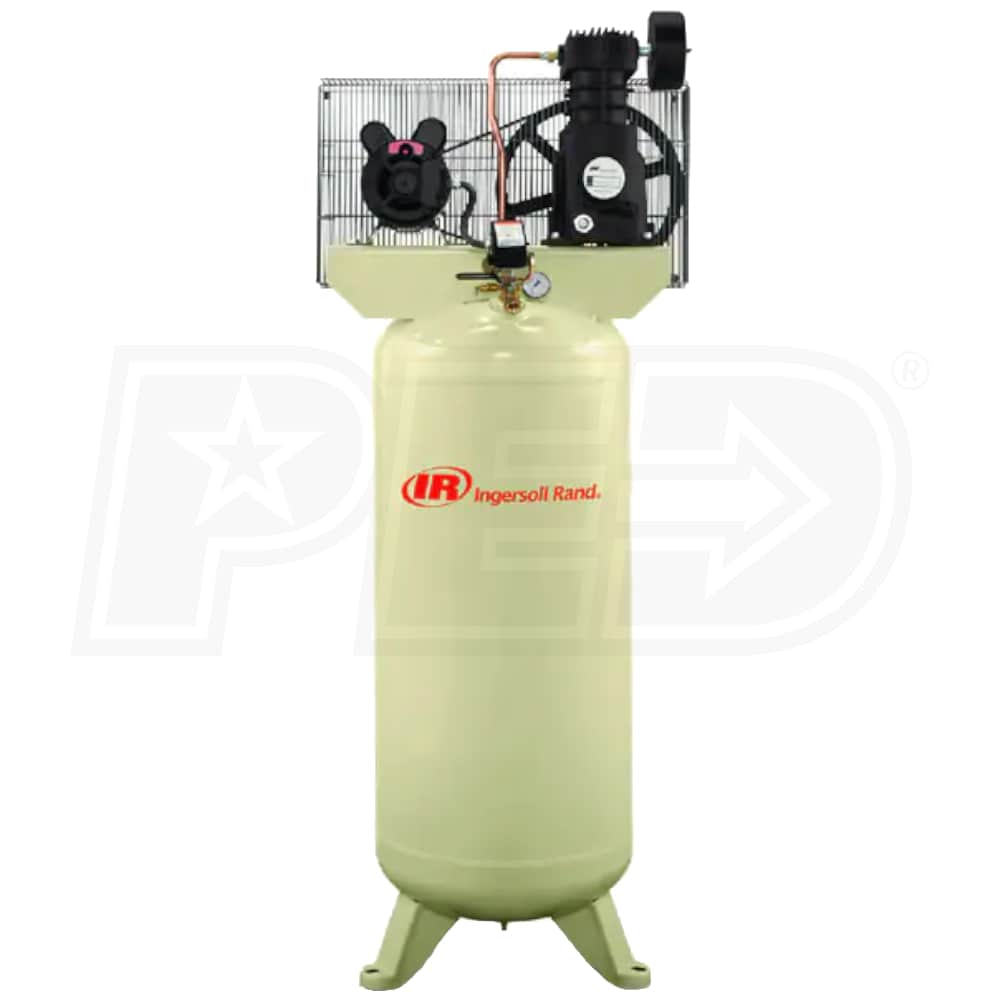

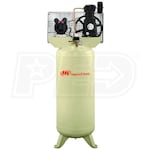
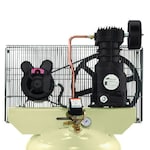
Customer Review Images
